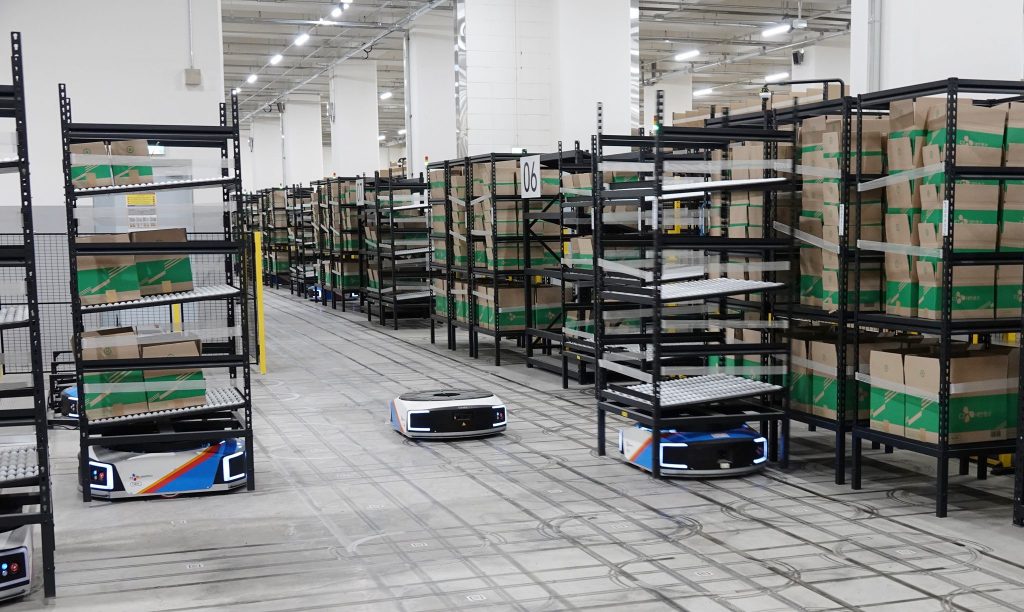
CJ Logistics announced that it has reduced the average size of its delivery box by 10% for products at its Gunpo Fulfillment Center by applying big data packaging technology. Big data packaging, a packaging technology unique to CJ Logistics, redesigns the box size based on volume data and product-specific order information to appropriately select boxes optimized for each order. Previously, all fulfillment centers used the same type of boxes. However, with the introduction of this technology, each center plans to use customized boxes.
CJ Logistics found nine optimized box sizes by combining 11.2 billion possible box sizes based on a set of data that included the type and quantity of products ordered by customers within a three-month period. The optimized boxes will be implemented at facilities in August, starting with Gunpo Fulfillment Center. Currently, about 75% of the boxes shipped from Gunpo Fulfillment Center are produced directly at the center, while the rest are shipped in boxes according to seller specifications.
Smaller delivery boxes reduce unnecessary empty space. Meaning fewer packaging materials will be used in each parcel. In addition, CJ Logistics has implemented a system to automatically select the optimal box for each order. With this system, wasted space is reduced and unnecessary overpackaging will be prevented, making the distribution process more eco-friendly.
Since the box size is smaller, it is possible to load more boxes into a delivery vehicle at one time. Hence, the capacity efficiency of delivery vehicles will increase.
On the other hand, CJ Logistics uses optimized boxes through its Smart Packaging System to increase work efficiency. Instead of workers assembling the boxes by hand, the system uses automated equipment that puts boxes directly into the logistics process. The worker can select the box size on the system, and the boxes will be automatically manufactured. Furthermore, the packaging solution recognizes and automatically fills empty space with packing materials before taping and labeling the completed parcels, accelerating efficiency while reducing product damage.
“Through systematic big data analysis, we are expecting to achieve both logistics efficiency and eco-friendly effects by reducing box sizes and utilizing fewer cushioning materials,” stated CJ Logistics TES (Technology, Engineering, Systems & Solutions) Innovation Center Management Leader Nam Gi-chan. “We will provide unique fulfillment services to our sellers and customers using our innovative technology.”