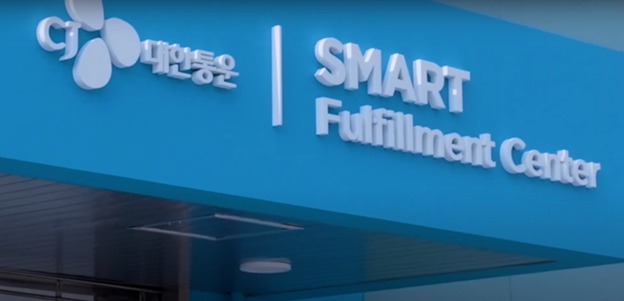
The Seamless World of Automated Logistics
E-commerce lets us order products straight to our doorsteps with ever-increasing speed and convenience.
But how exactly do these systems work? What are the technologies that make this process possible, and what is it like working in an environment powered by the world’s most cutting-edge e-commerce fulfillment automation technologies?
This week, CJ Newsroom explores CJ Logistics’ Gunpo Smart Fulfillment Center to find out more about CJ’s mission to boost productivity, efficiency and convenience by pioneering technology trends transforming future logistics.
CJ’s One-Stop E-commerce Center
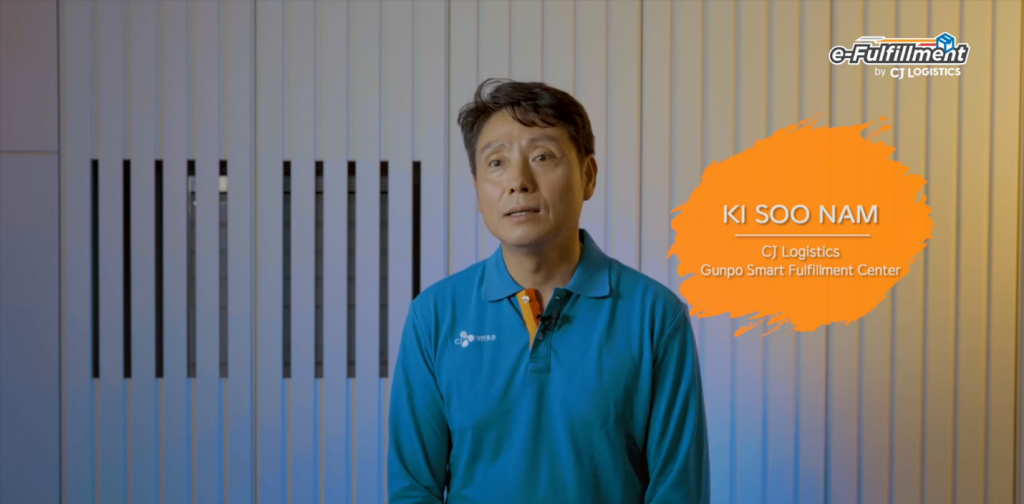
Fulfillment is at the heart of e-commerce competitiveness. Products need to be organized, packaged and sent to customers fluidly and safely, and CJ Logistics has committed a wide range of resources, research and talent to craft seamless smart fulfillment systems that makes it possible. The Gunpo Smart Fulfillment Center divides its fulfillment process into six stages: Inbounding, Receiving Orders, Picking, Inspection, Smart Packaging and Release.
“By integrating all the e-commerce logistics capabilities at our center – from warehousing to stocking to forwarding – our system is designed to be a one-stop-shop logistics process,” said Nam Ki-soo, Leader of CJ Logistics’s e-Commerce FC Team. “The main goal here is to provide solutions that incisively meet customer needs. By saving time and cost, we can add significant customer value.”
Inbounding – The Crucial First Step
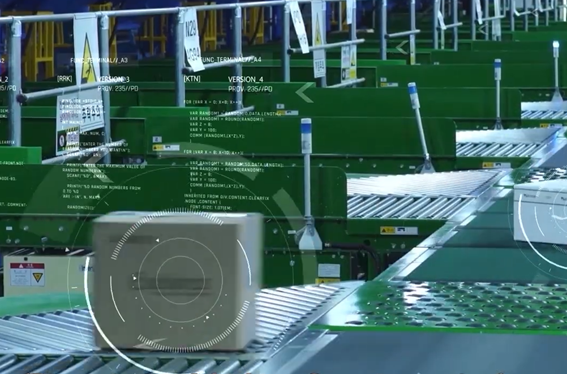
Inbounding is the first stage of the fulfillment center process. CJ’s advanced Dimension, Weighing and Scanning (DWS) system scans each product to electronically record its unique weight and proportions. Next, the staff load products onto Automated Guided Vehicles (AGVs), which spirit products away to the optimal storage location
“By introducing AGV use on the smart floor, we’ve been able to boost our productivity by 25%,” said Cho Joo-hyung, Director of the Gunpo Center. “We are quite possibly the first center in Korea to automate this much of the e-commerce process using AGVs.”
Receiving Orders & Picking – Pinpointing the Right Product
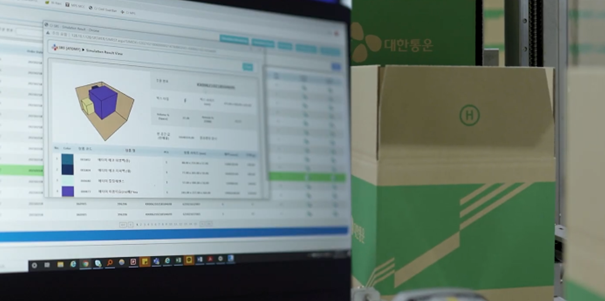
Once an order has been received, the E-commerce Integrated Logistics System (eFLEX) draws all the details it needs on the order’s status from roughly 50 seller platform and sends the order out into the fulfillment center. At this point, the product is located and forwarded to the box recommendation system for packaging.
Kim Min-seong from the center’s Release Team explained how the system keeps track of all kinds of variables. “eFLEX helps us to intuitively track a wide range of release processes at once,” he said.
Next up is the picking stage, which involves getting the right product into the right box. First, an automated case erector receives the product’s weight and size and automatically builds the ideal box to transport it in. It then shifts the box down the conveyor belt, where a unique barcode is printed on it.
Inspection & Smart Packaging – Checking, Securing, Refining
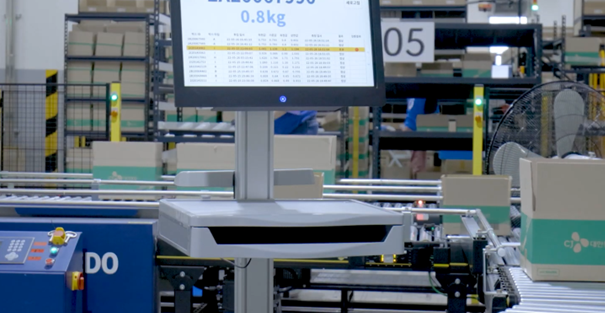
AGVs now move the products from the picking area to the release line. Boxes are weighed against their expected weight data and once the product has been inspected, it moves onto the penultimate stage: Smart Packaging.
Using 3D scanning, eco-friendly buffering material is automatically added to each box and fills out the box so the product will not bump around in transit. Once the taping machine has sealed up the box with eco-friendly tape and delivery labels, it is finally ready for release.
Release – Sending the Product Out Into the Big Wide World
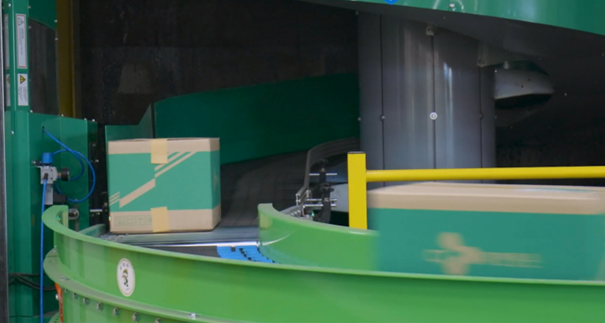
At the release stage, boxes are moved swiftly through a conveyor system. Each box passes under the Intelligence Scanner (ITS), which is mounted over the belt to assiduously process each delivery label and ensure the product is directed to the right region. When it reaches the appropriate junction on the conveyor, dynamic rollers beneath the box shift the package off the main belt and into the correct regional delivery area.
Amazingly this whole process – from the receiving of the order to the product arriving in the correct delivery section – takes only six hours. Thanks to this streamlined automated system, customers can place an order before midnight and see their parcel arrive the very next day.
The Future – Automated E-commerce Is Just Getting Started
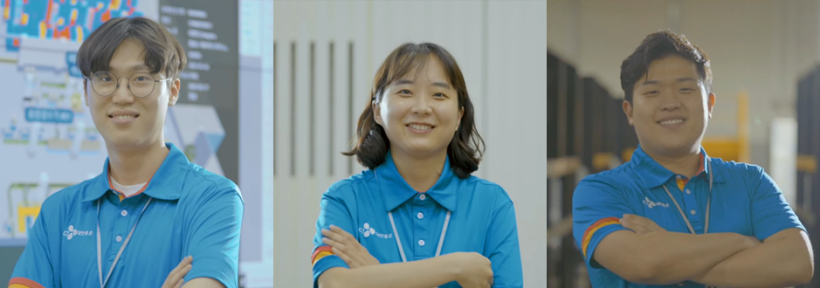
While all of the Gunpo Center’s technologies are highly advanced, CJ Logistics is constantly exploring new technologies and strategies to actualize the full potential of an automated eFulfillment future, where specialist employees and modern systems operate in harmony for greater efficiency and customer satisfaction.
“The future of CJ Logistics’ smart fulfillment is bright, and we will continue to work hard to provide our customers with tailored services and fast delivery,” said Cho Joo-hyung. “CJ Logistics will keep striving to become a leading company that innovates e-commerce in Korea.”