In an industry first, CJ Logistics is using specialized robots in its logistics operations. The innovative robotic equipment is capable of automatically lifting and moving boxes of different specifications without the need for employee intervention. CJ Logistics anticipates that the introduction of this new technology will increase both vendor and consumer satisfaction as the company can now handle various products from different shippers more efficiently through this advanced logistics technology.
AI Robotic Depalletizer Deployed at Dongtan Fulfillment Center Performs Picking Tasks Without Interruption
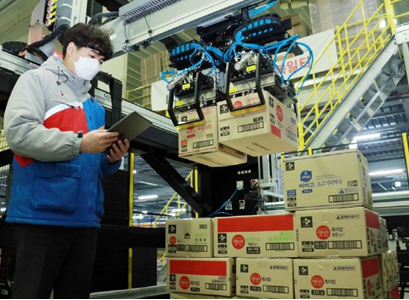
CJ Logistics announced on April 22, 2021, that the company has introduced artificial intelligence (AI) robotic depalletizers in its Dongtan Fulfillment Center in Gyeonggi-do, South Korea, becoming the first in the industry to adopt such technology. This machine identifies the area, height and location of boxes loaded on a pallet, automatically lifts the boxes and moves them to a conveyor belt. It is also referred to as an “unstructured pattern box-picking robot arm” due to its ability to automatically pick and lift boxes with different specifications even when they are piled up together or not properly aligned. The AI robotic depalletizer specializes in handling all kinds of logistics tasks related to picking products for e-commerce orders.
Existing robotic depalletizer technology could only be applied to boxes that fit an initial design structure, meaning that the robots could exclusively lift boxes matching previously-determined specifications and making it impossible for it to perform tasks if the boxes moved from their designated position. Despite a growing diversification of consumers’ ordered products, picking robots were mainly utilized in logistics centers that handle a single type of product due to its lack of task flexibility. In other centers, managers were left with no other option than to move heavy loads using manpower instead of robots.
Application of 3D Image Sensor and AI Deep Learning Technology
CJ Logistics has applied 3D image sensors and AI deep learning technology in order to materialize a system that can consecutively handle boxes that vary in size and shape. The vision camera installed in the upper part of the system photographs the area, height and corner position of the box in real time, recognizes those values as data and independently evaluates them, performing picking tasks according to the state and condition of each box. Despite differences in height or shape among the boxes stacked on a pallet, the equipment can seamlessly perform its tasks by simultaneously lifting up to two boxes in each pass, upping the distribution center’s capacity for productivity.
The equipment can also lift loads up to 20 kg at a time by using vacuum absorption technology and a specialized pad attached to the end of the robot’s arm. After the vacuum feature is deployed, the support fixture safely backs up both sides of the box to prevent shaking or falling while transferring the load. This machine can move an average of 700 boxes per hour.
CJ Logistics plans to continue actively developing cutting-edge technologies that are highly advantageous in logistics operations, improving the working environment of its employees and further increasing productivity.
“By handling various types of products more efficiently through the use of AI robot depalletizers, we became capable of providing an advanced fulfillment service,” said an official from CJ Logistics. “We will strive to lead the logistics industry through our advanced logistics technologies and their on-site implementation.”