CJ Logistics and Starbucks Korea set a new standard in coffee logistics with advanced facilities and technology
Did you know that Koreans are the biggest coffee lovers in Asia? According to market research firm Euromonitor, Koreans consumed 405 cups of coffee per person on average last year, more than double the global average of 152 cups.
At the heart of Korea’s “Coffee Republic” is CJ Logistics. Starbucks, the country’s leading coffee chain, relies on CJ Logistics for its coffee supply chain. Every day, CJ Logistics delivers fresh coffee to 1,937 Starbucks stores across the country. Explore the fascinating collaboration between the top names in coffee and logistics and how a cup of coffee makes its way into the hands of people everyday.
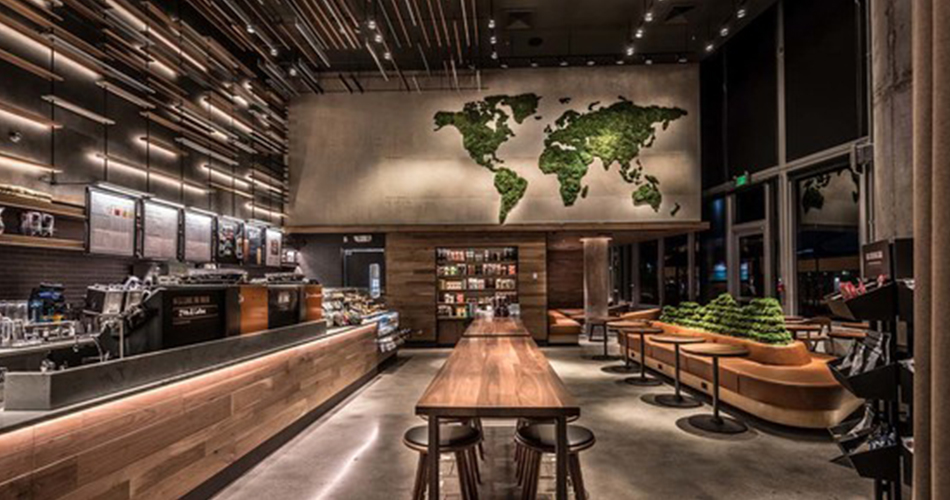
Becoming a Global Standard in Coffee Logistics
The key to great coffee lies in the “beans.” Factors like bean freshness, temperature, and humidity are vital in coffee flavor. Starbucks roasts beans in the U.S. using its special expertise and ships them to each market. Here, speed of delivery matters to ensure a consistent coffee experience worldwide. This makes precise distribution management and strict adherence to logistics standards essential.
Since 2012, CJ Logistics has built a strong partnership with Starbucks Korea, establishing itself as the most reliable logistics provider. CJ Logistics uses specialized infrastructure and expertise to maintain the ideal temperature from arrival through delivery.
CJ Logistics’ Tailored Strategy for Coffee Bean Freshness
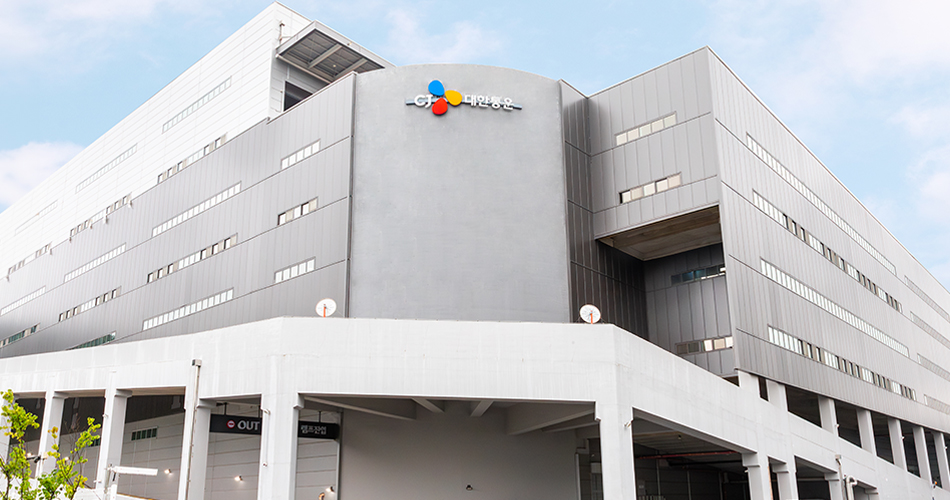
In 2015, CJ Logistics opened the Deokpyeong Starbucks Center in Icheon, Gyeonggi Province, a facility dedicated exclusively to Starbucks’ logistics services. Equipped with a “three-temperature zone automated management system” capable of handling refrigeration, freezing, and room temperature environments, the center offers fully optimized logistics services for Starbucks.
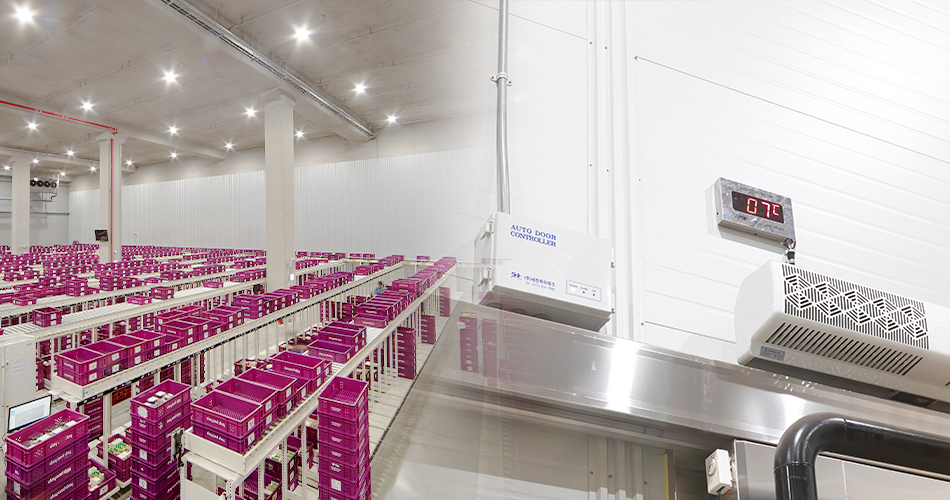
Building on the successful operation of the Deokpyeong Starbucks Center, Starbucks has continued to expand in Korea, strengthening its logistics competitiveness. To support this growth, CJ Logistics and Starbucks Korea opened their largest logistics hub, the “Busan Starbucks Center,” near Busan New Port and Garak Interchange in 2022.
As a key entry point handling 93% of coffee beans imported to Korea, Busan Port is essential for preserving the freshness of Starbucks products. The Deokpyeong Starbucks Center manages logistics for the metropolitan and central regions, while the Busan Starbucks Center oversees logistics for the southern region, covering Gyeongsang and Jeolla provinces, and is responsible for Starbucks’ logistics operations nationwide.
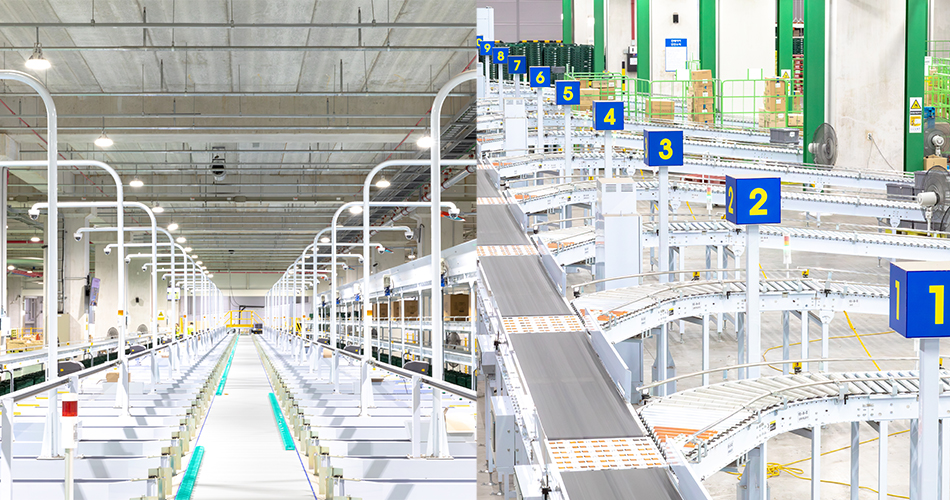
Cutting-edge Logistics Technology and Infrastructure Reducing Delivery Time by 90%
The Busan Starbucks Center is the largest coffee-dedicated logistics facility in South Korea, spanning approximately 38,000 square meters, equivalent to six soccer fields. This vast facility operates like a massive refrigerator, with a temperature-controlled system managing room temperature, refrigeration, and freezing environments.
From here, the products are quickly delivered to stores using a cold chain (temperature-controlled logistics) vehicle. This system ensures the timely delivery of coffee beans, desserts and delicate items such as fruits and salads to Starbucks nationwide. Goods requiring room temperature storage, like napkins and other supplies, are also stored and managed here.
The technical efforts to accelerate the product “picking” process are crucial. Storing tens of thousands of items across different temperature zones, the Busan Center dedicates approximately 70% of order-to-shipment time to picking, given the variations in products and quantities each store orders.
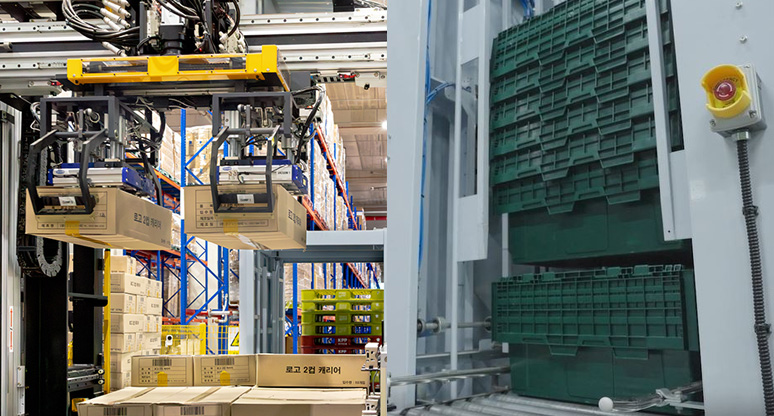
To address this challenge, CJ Logistics has introduced advanced automated logistics technologies. These include the “Auto Sorter,” which automatically sorts products by delivery area, and the “Robot Arm Depalletizer,” which moves loaded boxes onto the conveyor belt. Additionally, there are the “Multi Picking System (MPS),” an automated system that inserts products into boxes, and the “Piece Assorting System (PAS),” which automatically sorts products by store.
These technologies operate far faster and more accurately than manual handling, eliminating the need for additional inspection and re-sorting at stores. As a result, logistics processing time has been reduced dramatically, from 90 minutes to just 10, significantly enhancing operational efficiency.
“Thanks to these logistics technologies, we can offer an optimized and customized service for the entire delivery process, from the logistics center to the store and ultimately to the customer,” said Jang Jun-seok, Director of CJ Logistics Busan Starbucks Center. The stability and advanced services provided across all logistics form the foundation of CJ Logistics’ competitiveness and the trust it has earned from its customers.